Kako bi uvođenje 5S izgledalo što demonstrativnije, poduzeća
prakticiraju zamoliti radnike da se sav nepotrebni materijal i nered odlože na
jednu gomilu. Najčešće će ta gomila biti izuzetno velika i vrlo lako će privući
pažnju svih radnika. Zatim se sprovodi veliko čišćenje podova od prašine,
masti, ulja i ostale prljavštine. Poslije toga se sve mašine čiste i glancaju.
Najčešće će biti toliko prljavštine i otpada da radnici brzo shvate koliko je
vođenje računa o radnom okruženju neophodno.
ponedjeljak, 11. veljače 2013.
32. IMPLEMENTACIJA 5S
petak, 8. veljače 2013.
31. 5S
5S je skup pravila za organizaciju radnog mjesta svakog radnika. Cilj
je da svako radno mjesto bude organizirano tako da bude maksimalno efikasno i
ubrza i olakša rad radniku. 5S je sigurno najprepoznatljivija tehnika LEAN
koncepta, jer ju je najlakše primijeniti i rezultati bivaju vidljivi gotovo
trenutno. Preko 5S pravila organizacije radnog prostora najlakše se svim
zaposlenicima objašnjava čitava LEAN filozofija eliminacije gubitaka u
poduzeću.
5S sprovode timovi i redovna je praksa da manageri ocjenjuju i nagrađuju najbolje timove na mjesečnom nivou. Potrebno je istaknuti da 5S ima jako bitnu ulogu kod sigurnosti na radnom mjestu, tako da i taj dio manageri ocjenjuju (npr. ako u 3 mjeseca ne bude nikakvog sigurnosnog incidenta, radnici dobivaju premiju). 5S iz LEAN koncepta potiču iz japanskog jezika tako da 5 japanskih riječi na slovo S opisuju načela 5S tehnike:
Seiri – Sort – sortiranje
Seiton – Straighten – red
Seiso – Scrub – čišćenje
Seiketsu – Standardite – standardizacija
Shisuke – Sustain – samodisciplina
Seiri – Sort – sortiranje
-
potrebno je identificirati sve stvari nepotrebne
za rad, odnosno proizvodnju i eliminirati ih iz radnog prostora
-
odabrati alat neophodan za rad
-
alat i materijali koji nisu često korišteni
spremiti u zasebna spremišta
-
stvari koje se uopće ne koriste baciti
-
na samo da je pogon očišćen od smeća, zastarjelih
predmeta, naprava, otpada i sl., već je oslobođen prostor i lakše je pronaći
potrebne stvari
Seiton – Straighten – red
-
stvari moraju biti sistematski posložene, tako da
ih možemo jednostavno koristiti, te da ih svatko može lako pronaći
-
alati koji se koriste zajedno, moraju biti i
smješteni zajedno
-
često korišten alat mora biti smješten u blizini
mjesta gdje se koristi
-
etiketiranje: bez označavanja se vrlo lako
zaboravlja gdje stvari stoje
-
ergonomija: često korišten alat treba biti
smješten na lako dostupnom mjestu i da se izbjegne nepotrebno saginjanje,
istezanje ili pretjerano hodanje
-
stvari kasnije treba jednostavno vratiti na
njihovo mjesto – posebno je bitno da označavanje bude razumljivo i jednostavno
-
često korištena oprema, alat i materijali, a
naravno i njihovo mjesto skladištenja moraju biti jasno označeni
Seiso – Scrub – čišćenje
-
stvari i radni prostor treba održavati i čistiti;
otpad i prljavština na radnom mjestu su neprihvatljivi
-
nije dovoljno jednom očistiti i urediti radni
prostor i pribor
-
nužno je redovno čićenje, obično na dnevnoj bazi,
jer se u suprotnom sve vraća na staro
Seiketsu – Standardite – standardizacija
-
u ovom koraku uspostavljamo standardne rutine i
pretvaramo ih u navike
-
jedan od najvećih problema je kako izbjeći
vraćanje starim navikama
-
za početak je dobro postaviti pisane standarde
-
najbolje je napraviti procedure na plakatima
(uočljivi natpisi)
Shisuke – Sustain – samodisciplina
-
sustain ili samodisciplina je najkompleksniji
zadatak jer nije dovoljno povremeno počistiti radno mjesto kako bi odali dojam
organizacije i čistoće, već je potrebno održavati taj red i prilagođavati se
novonastalim uvjetima
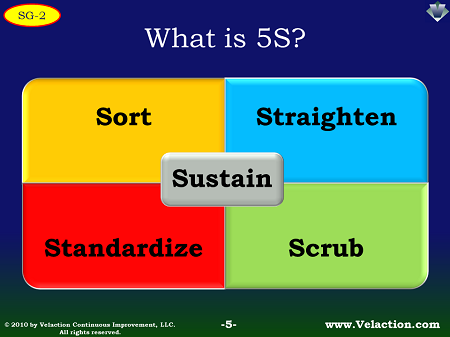
ponedjeljak, 4. veljače 2013.
30. TOTALNO PRODUKTIVNO ODRŽAVANJE (Total Productive Maintenance)
Otkazi mašina su jedan od najvećih problema u LEAN proizvodnji.
Pouzdanost opreme u proizvodnim postrojenjima je izuzetno značajna jer je
dovoljno da jedna mašina otkaže, pa da dođe do zaustavljanja cijele proizvodne
linije. Važan alat za minimiziranje pojave otkaza u procesu proizvodnje je
„totalno produktivno održavanje“. LEAN proizvodnja teži ka 100 % pouzdanosti i
dostupnosti opreme.
-
potrebne najbolje procedure za održavanje,
-
informacije o otkazima od kojih se prave šeme
otkaza mašina,
-
visoko obučeni radnici koji u najkraćem vremenskom
roku mogu održavati mašine.
UEO = E x K x U
Gdje je:
UEO = ukupna efikasnost opreme,
E = efikasnost opreme,
K = koeficijent učinaka,
U = učešće dobrih proizvoda.
-
efikasnosti opreme 90 %,
-
koeficijent učinaka 95 %,
-
učešće dobrih proizvoda 99 %,
-
sveukupni UEO = 85 %.
1)
Iznenadni otkazi,
2)
Gubici zastoja – otkaza,
3)
Postavljanje i podešavanje opreme,
4)
Prazni hodovi i mali zastoji,
5)
Gubici efikasnosti (brzine rada),
6)
Smanjenje stvarne brzine rada.
Primjena totalnog produktivnog održavanja
Totalno produktivno održavanje je našlo primjenu i van proizvodnje.
Zanimljivo je da poznati svjetski lanac brze hrane McDonalds upravo koristi
TPM. Svakodnevno se sve mašine rastavljaju , čiste i podmazuju kako ne bi došlo
do otkaza i kako kupac ne bi čekao duže na hranu, s obzirom da je osnovna
osobina takvih restorana brzina. TPM je našlo primjenu u bolnicama gdje se vrši
i preventivno i korektivno održavanje operacione opreme i opreme za dijagnozu
kako se ne bi dešavalo da uređaji otkažu baš kad je potrebno. Filozofija TPM-a
je iskorištena i kod avio kompanija. Pored toga što se avioni održavaju u
skladu sa preventivnim održavanjem veće su i kaizen aktivnosti i korektivno
održavanje je od velike koristi. Jedna od najvećih avio kompanija u USA
Southwest Airlines koristi isključivo jednu vrstu aviona i to BOEING 737, avion
srednje veličine. Korištenjem jednog modela u mnogome se smanjuju troškovi
održavanja i smanjuje pasiva, jer nema potrebe držati na lageru veliki broj
različitih dijelova različitih proizvođača, a svi avioni su uvijek spremni.

Pretplati se na:
Postovi (Atom)